Technology
Manufacturing process of DWI can
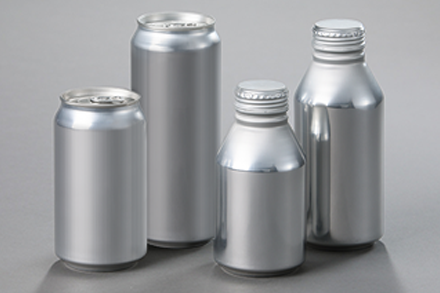
A two-piece can made with DWI (drawn and wall ironed) can forming method invented in the U.S. in 1958. It has been widely used in Japan since 1971.
DWI can is made from aluminum or tinplate coil sheet which is drawn into cup shape and then wall-ironed into a can shape with several stages of wall ironing process.
It is mainly used for beer and carbonated soft drink (CSD) and for some aerosol products.
The can bottom is dome-shaped to withstand internal pressure, and the entire can body surface can be printed.
The can forming method takes advantage of the ductility of metal, enabling the sidewall to be as thin as 0.1 mm and the can weight to be lighter than 3-piece cans. Especially in the case of aluminum DWI can, its sidewall can be extremely thin and the total can weight can be very light. Recently, there have been more beverage cans with smaller diameter ends.
Can making process of 2-piece (DWI) can
- Uncoiler
- Uncoil can stock coil.
-
- Lubricator
- Apply lubricant.
-
- Cupping press
- Stamp out coil sheet into cup shape.
- Bodymaker
- Thin down can body sidewall with the draw and wall ironing process using coolant and forms the bottom.
- Trimmer
- Trim down the top edge of can sidewall to a specified can height.
-
- Washer
- Wash off coolant and dry the can.
- Coater/Printer
- Coat and print can surface, apply overvarnish and dry and bake the can.
-
- Spray machine
- Apply can internal coating.
-
- Oven
- Dry and bake the can.
- Necker/Flanger
- Narrow down and flange can top.
-
- Can inside and outside inspection device
- Inspect defects on can inside and outside.
- Palletizer
- Pile up cans on pallets.
- End seaming (by customers)
Can forming process by bodymaker
Flat sheet is formed into a cup shape, which is then processed by the bodymaker.
The cup is drawn into can shape by bodymaker punch.
There are three wall ironing stages.
Can body bottom is formed.
Can body top edge is then trimmed.
Contact us
Return to Technologies